Overview
Polytech magnetic separators have been designed to remove ferrous and non-ferrous solid contaminants from coolants and oils.
Magnetic separators can substantially reduce filter cartridge consumption and element changes when used in grinding, honing and lapping operations where filter cartridges are used. They can reduce the concentration of small fines left in the coolant by chip conveyors in broaching, milling and drilling operations that can settle in tanks and reduce machine tool life.
Applications
- Creepfeed Grinding
- Surface Grinding
- Internal & Centerless Grinding
- End Mill Grinding
- Honing, Lapping, & Superfinishing
- Broaching, Hobbing, Trepanning
- Gear Hobbing
- Boring, Drilling
- Chucking, Milling
- Turning, Lathes, Machining Centers
How it Works
The magnetic drum is made up of alternating permanent magnets and steel discs. The magnetic field is extended by the magnetized steel discs to maximize effectiveness without resorting to more costly high strength or rare earth magnets. A comb type scraper and adjustable discharge chute optimizes sludge removal.
Design and Customization
Speak to one of our engineers about your application's specific requirements.
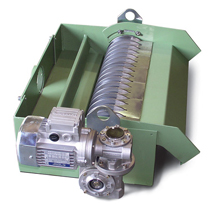
Specifications
Model | Flow Rate (GPM) Water |
Flow Rate (GPM) 40 SSU Oil |
Drawings |
MSE3 | 13 | 6 | ![]() |
MSE5 | 26 | 13 | ![]() |
MSE7 | 65 | 32 | ![]() |
MSE10 | 79 | 40 | ![]() |
MSE15 | 106 | 53 | ![]() |
MSE20 | 132 | 56 | ![]() |
* Higher flow rate available upon request